Kaizen (continuous improvement) Skill Overview
Welcome to the Kaizen (continuous improvement) Skill page. You can use this skill
template as is or customize it to fit your needs and environment.
- Category: Technical > Continuous Integration/Continuous Deployment
Description
Kaizen, a Japanese term meaning 'change for the better', is a philosophy that focuses on continuous improvement in all aspects of life, but it's often applied to business and manufacturing processes. It involves everyone in an organization, from top management to frontline workers, in identifying small, incremental changes that can improve efficiency and productivity. Techniques used in Kaizen include problem-solving tools like fishbone diagrams and Pareto charts, process mapping, and the 5S methodology (Sort, Set in order, Shine, Standardize, Sustain). The ultimate goal of Kaizen is to create a culture where improvement is ongoing and embedded in daily operations.
Expected Behaviors
Micro Skills
Understanding the Japanese origin of Kaizen
Grasping the business interpretation of Kaizen
Understanding the focus on employee involvement
Grasping the concept of continuous improvement
Understanding the principle of 'Go See'
Grasping the principle of 'Ask Why'
Learning the principle of 'Show Respect'
Recognizing the impact on efficiency
Grasping the benefits for customer satisfaction
Recognizing successful Kaizen in case studies
Grasping the role of continuous improvement in industry leaders
Understanding the link between improvement and competitiveness
Grasping the importance of adaptability
Learning to spot waste
Grasping the concept of value and non-value added activities
Learning to question the status quo
Grasping the concept of 'Gemba'
Understanding the importance of critical thinking
Grasping the concept of '5 Whys'
Understanding the concept of waste in Kaizen
Identifying types of waste in a given process
Applying the principle of 'Just in Time' production
Implementing the 'Jidoka' or 'automation with a human touch' principle
Identifying areas for improvement
Developing a plan for implementing improvements
Executing the improvement plan
Monitoring the results of the implemented improvements
Understanding the purpose and structure of a Kaizen event
Contributing ideas and suggestions during the event
Working collaboratively with other team members
Following through on tasks assigned during the event
Understanding the five steps of the 5S methodology: Sort, Set in order, Shine, Standardize, Sustain
Applying each step of the 5S methodology to a specific work area
Maintaining the improvements made through the 5S methodology
Training others in the 5S methodology
Identifying team members for the initiative
Setting clear objectives for the initiative
Planning and executing the initiative
Monitoring progress and making necessary adjustments
Understanding the current process
Identifying bottlenecks or inefficiencies in the process
Proposing potential improvements
Evaluating the impact of proposed improvements
Defining the steps in the procedure
Training staff on the new procedure
Monitoring compliance with the procedure
Making adjustments to the procedure as needed
Understanding how to create and interpret fishbone diagrams
Applying fishbone diagrams to identify root causes of problems
Understanding how to create and interpret Pareto charts
Using Pareto charts to prioritize improvement efforts
Identifying project scope and objectives
Developing a detailed project plan
Coordinating internal resources and stakeholders for flawless execution
Tracking project performance using appropriate systems, tools and techniques
Managing changes to the project scope, schedule, and costs
Understanding different learning styles and adapting training accordingly
Creating engaging learning materials and experiences
Assessing trainee understanding and providing feedback
Evaluating training effectiveness and making necessary adjustments
Understanding and documenting current processes
Identifying bottlenecks and areas for improvement
Designing new or improved processes
Communicating changes and ensuring they are implemented correctly
Collecting and organizing relevant data
Applying appropriate statistical methods to analyze data
Interpreting results and drawing conclusions
Using findings to inform process improvements
Promoting the importance of continuous improvement
Encouraging employee participation in Kaizen events
Rewarding and recognizing improvements
Incorporating Kaizen principles into company policies and procedures
Aligning Kaizen initiatives with business objectives
Incorporating Kaizen principles into strategic planning processes
Evaluating the potential impact of Kaizen initiatives on business performance
Prioritizing Kaizen projects based on strategic importance
Identifying opportunities for major process overhauls
Developing detailed plans for process redesign
Managing the implementation of complex process improvements
Monitoring and adjusting process improvements post-implementation
Establishing metrics to measure the success of Kaizen initiatives
Collecting and analyzing data on Kaizen performance
Identifying areas where Kaizen initiatives are not meeting expectations
Making necessary adjustments to improve the effectiveness of Kaizen initiatives
Tech Experts
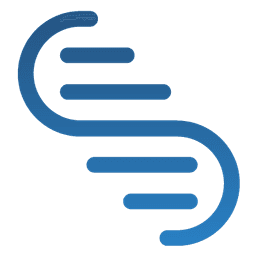
StackFactor Team
We pride ourselves on utilizing a team of seasoned experts who diligently curate roles, skills, and learning paths by harnessing the power of artificial intelligence and conducting extensive research. Our cutting-edge approach ensures that we not only identify the most relevant opportunities for growth and development but also tailor them to the unique needs and aspirations of each individual. This synergy between human expertise and advanced technology allows us to deliver an exceptional, personalized experience that empowers everybody to thrive in their professional journeys.